How to Get Predictable and Reliable Linear Motion
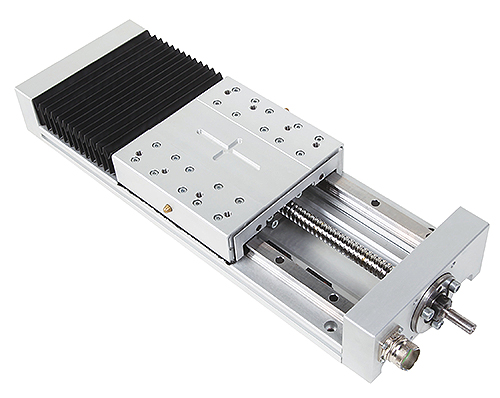
Theoretically, it might appear a very easy thing to choose the right linear actuator for someone to use to finish a particular assignment. However, there is more to actuator selection than most people, including the specialists, consider. One thing for sure is that underperforming or faulty actuators come about as a result of the systematic error in their specifications during setup. The efficiency and quality of an actuator is defines by four main parameters. First is the nature of the infrastructural layout onto which the actuator is to be laid. This basically plays an important role in ensuring that the actuator is well positioned. The infrastructural layout entails the space to do this too.
The second one is the converter which transforms the rotational motion into linear motion for the flexibility and versatility of the actuator. This converter usually comes along with a number of distinct components as well. The third one is a component that protects the carriage from suffering the dangers of friction, which are wear and tear, during motion that is usually linear. This component has a maximum load capacity and longevity. The final component is a fully mobile carriage that adequately and safely anchors the other pars, such as the camera and optics. There are a total of eight objectives for the design as below:
1. Potential.
This is the capability of the actuator, the amount and type of load it can withstand comfortably without malfunctioning. This addresses the two lads namely the dynamic and static loads, in addition to the bending moment and thrust. This goes down to the very fine details of how the actuator was made by the manufacturer.
2. Accuracy and Repeatability.
To avoid the risk of over specification and overpayment, it is important to know the actuator’s ability for motion. Accuracy is in most cases an absolute parameter for most actuators, while repeatability is the most vital. Repeatability can take either one or two directions and therefore gauges the ability of the system to handle load from either directions. Accuracy is dictated by two aspects, positioning and distance covered. Just like a micrometer screw gauge, readings of accuracy are in terms of thousandths of an inch.
3. The distance of movement.
Also known as the stroke, it’s measured in inches. It also includes the safety stroke. One important thing to note is that there is a distinction between the stroke and the overall length.
4. Utility.
This is simply the duty cycle, or the number of cycles that the machine makes per minute. This is a specification that defines the expected total usage of the actuator. They also help determine how much it can work before being serviced. They come with the specifications or can be taken from the manufacturer.
5. Serene Surroundings.
Serenity in surrounding covers every aspect that makes up the actuator’s working environment. These are characterized by the humidity and temperature levels, the presence, nature and amount of pollutants as well as corrosive compounds, and finally, the cleanliness levels. Therefore, one should be very keen to note these aspects of the environment, and be quick to use any protective seals to guard the actuator against such extremities. In the case that the actuators have no protective gears, one should be prompt in communication with the supplier.
6. The time.
This is a parameter that is more often than not, ignored by virtually every player, be it the designers or engineers. It is important that at the beginning of it, the project timelines should be clearly spelt out, so as to have a clear frame of what is required. Having the timeline well-known supplements the knowledge in the size of the budget. An actuator should perfectly fit into the expected timeline of the project, and therefore, knowing the tidbits of the expected completion time in key. These include having knowledge of the production schedules and quotations. Any actuator, however good, can be rendered inadequate if its operation doesn’t match its timeline.
7. Inclination.
Selection of the most ideal actuator is reliant upon the manner in which it will fit into the available space. This inclination dictates the weight of the load and the subsequent amount of force to push to through. As a result, there is the additional need to determine the position of the carriage, since it determines the inclination of the load. Any inclination is possible, be it vertical or horizontal, as long as there is application of some geometry. It is worth noting however, that these differences in inclinations are what determine the type and nature of actuator, since they highlight the strength of the actuator. If the actuator is made of more than one axis, it is important that it is fixed tightly and with protective plates, so as to prevent unwanted vibrations and mismatches.
8. Rates.
The rates here simply stand for the speeds that the machines are expected to go at. It is essential that one selects the actuator depending on the nature of the task that he or she is going to undertake. Some machines move faster while others slower. Therefore one should be able to match up the amount and type of work, with the capability of machine.